How Alcast Company can Save You Time, Stress, and Money.
How Alcast Company can Save You Time, Stress, and Money.
Blog Article
3 Simple Techniques For Alcast Company
Table of ContentsNot known Facts About Alcast CompanyGetting My Alcast Company To WorkThe Main Principles Of Alcast Company The Ultimate Guide To Alcast CompanyAbout Alcast CompanyRumored Buzz on Alcast Company
Chemical Contrast of Cast Light weight aluminum Alloys Silicon promotes castability by minimizing the alloy's melting temperature and improving fluidity throughout spreading. Additionally, silicon contributes to the alloy's toughness and wear resistance, making it valuable in applications where toughness is important, such as auto components and engine elements.It likewise enhances the machinability of the alloy, making it simpler to refine right into finished items. By doing this, iron contributes to the overall workability of aluminum alloys. Copper raises electric conductivity, making it beneficial in electric applications. It additionally enhances corrosion resistance and includes in the alloy's overall stamina.
Manganese contributes to the stamina of light weight aluminum alloys and improves workability (aluminum metal casting). It is typically used in wrought light weight aluminum items like sheets, extrusions, and accounts. The presence of manganese aids in the alloy's formability and resistance to cracking throughout construction processes. Magnesium is a lightweight element that supplies strength and influence resistance to light weight aluminum alloys.
Fascination About Alcast Company
It allows the production of lightweight parts with excellent mechanical residential or commercial properties. Zinc improves the castability of aluminum alloys and helps regulate the solidification procedure during casting. It improves the alloy's stamina and firmness. It is typically discovered in applications where complex shapes and fine information are necessary, such as attractive spreadings and specific automotive components.

The key thermal conductivity, tensile stamina, yield toughness, and elongation differ. Among the above alloys, A356 has the highest thermal conductivity, and A380 and ADC12 have the least expensive.
8 Simple Techniques For Alcast Company
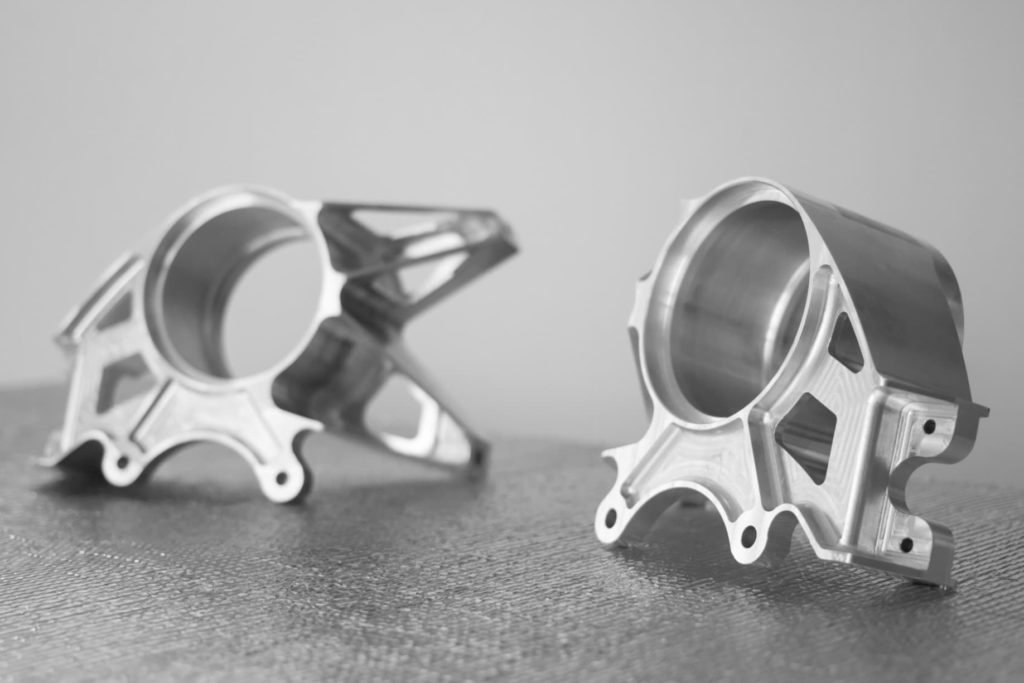
In accuracy spreading, 6063 is fit for applications where elaborate geometries and high-quality surface Resources coatings are paramount. Examples consist of telecommunication rooms, where the alloy's remarkable formability permits sleek and cosmetically pleasing layouts while keeping structural integrity. Similarly, in the Lights Solutions sector, precision-cast 6063 elements develop elegant and reliable lighting components that call for detailed shapes and good thermal efficiency.
The A360 exhibits remarkable prolongation, making it perfect for complex and thin-walled components. In precision casting applications, A360 is appropriate for industries such as Customer Electronics, Telecommunication, and Power Devices.
Fascination About Alcast Company
Its one-of-a-kind residential or commercial properties make A360 an important selection for precision casting in these sectors, boosting product durability and quality. Light weight aluminum alloy 380, or A380, is a commonly made use of casting alloy with a number of distinctive features. It offers outstanding castability, making it a perfect selection for accuracy casting. A380 exhibits excellent fluidity when molten, guaranteeing detailed and thorough mold and mildews are properly replicated.
In precision casting, aluminum 413 shines in the Customer Electronics and Power Equipment sectors. This alloy's exceptional deterioration resistance makes it an exceptional choice for outdoor applications, ensuring resilient, long lasting products in the discussed industries.
Getting My Alcast Company To Work
When you have decided that the aluminum die casting process is appropriate for your job, a critical following action is picking one of the most suitable alloy. The aluminum alloy you pick will substantially impact both the casting process and the properties of the last item. Since of this, you must make your decision meticulously and take an educated strategy.
Determining one of the most suitable light weight aluminum alloy for your application will indicate weighing a vast range of attributes. These relative alloy features comply with the North American Die Spreading Organization's standards, and we've split them right into 2 categories. The very first classification addresses alloy attributes that affect the manufacturing procedure. The 2nd covers qualities impacting the properties of the end product.
Our Alcast Company Ideas
The alloy you select for die casting straight affects numerous facets of the casting procedure, like just how very easy the alloy is to work with and if it is prone to casting defects. Hot splitting, likewise known as solidification fracturing, is a common die casting issue for light weight aluminum alloys that can lead to internal or surface-level rips or splits.
Particular aluminum alloys are much more vulnerable to hot fracturing than others, and your selection ought to consider this. One more common problem discovered in the die spreading of aluminum is die soldering, which is when the actors stays with the die walls and makes ejection hard. It can damage both the cast and the die, so you must look for alloys with high anti-soldering properties.
Deterioration resistance, which is currently a notable feature of aluminum, can differ significantly from alloy to alloy and is an essential characteristic to take into consideration relying on the ecological conditions your product will certainly be subjected to (Casting Foundry). Wear resistance is one more home commonly sought in light weight aluminum products and can distinguish some alloys
Report this page